Projects
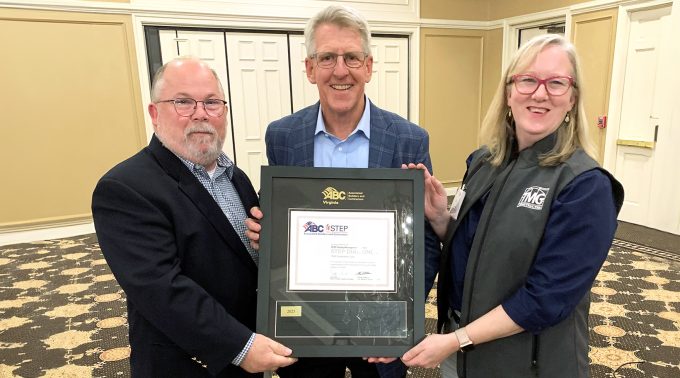
Award Winning Safety
The very first tenet expressed in TMG’s Values Statement is “Safety Matters.” Using this statement as a guiding principle, TMG has developed an award-winning safety record driven by training and attention to detail.